Why Double-Sided Tape Does Not Adhere Well to PLA in FDM 3D Printing and How Fusionar Solved It
In Fused Deposition Modeling (FDM) 3D printing, using double-sided tape to bond PLA-printed objects presents significant challenges. PLA (Polylactic Acid) is a widely used thermoplastic known for its ease of printing, but its surface properties make adhesion with certain tapes difficult.
Why Double-Sided Tape Struggles to Adhere to PLA
- Smooth Surface of PLA PLA surfaces are often smooth and non-porous, reducing the effective contact area for adhesives and weakening the bond.
- Low Surface Energy PLA has a surface energy that may not be compatible with many pressure-sensitive adhesives, leading to weak adhesion.
- Adhesive Compatibility Issues Many double-sided tapes are formulated for materials like metals, glass, or ABS, and do not interact well with PLA’s molecular structure.
Traditional Methods to Improve Adhesion
- Surface Preparation (Sanding or Texturizing) Increasing surface roughness can enhance adhesion by providing more bonding points. However, this process can be labor-intensive and affect part dimensions.
- Using Primers or Adhesion Promoters Chemical treatments can improve adhesion, but they introduce additional materials and may not be suitable for all applications.
Fusionar's Innovative Solution
At Fusionar, we have developed a new proprietary methodology that overcomes the limitations of traditional adhesion techniques. Our solution significantly enhances the bonding strength between double-sided tape and PLA without compromising the integrity of the printed part.
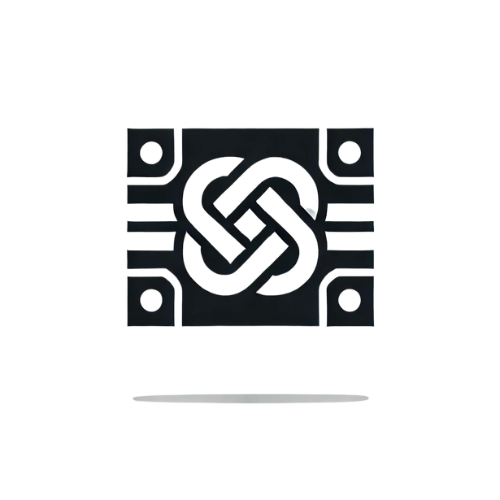
Stronger and More Reliable Adhesion
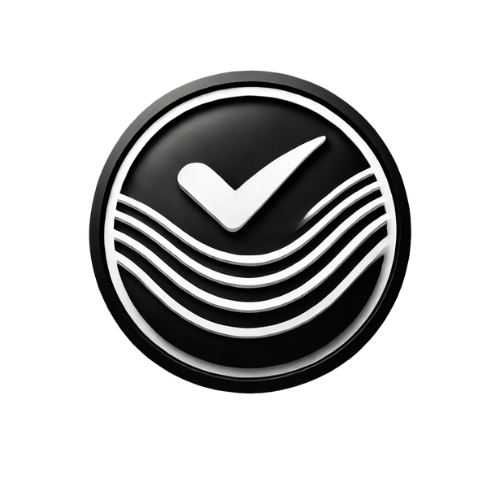
No Need for Additional Surface Treatments
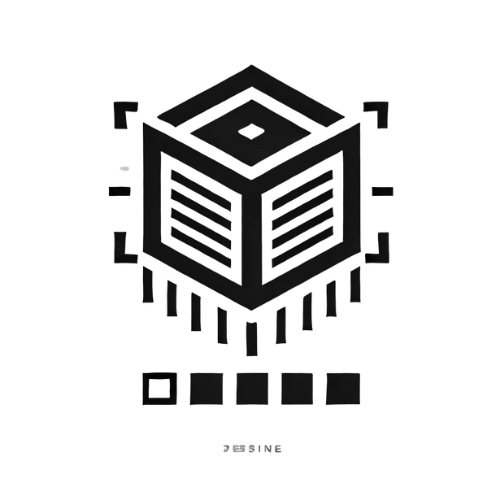
Maintains Print Accuracy and Aesthetic Quality
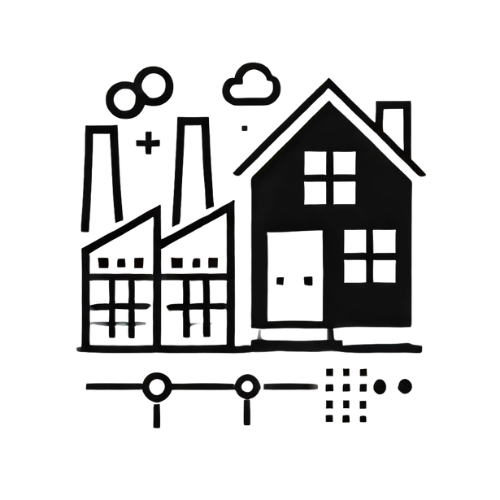
Optimized for Industrial and Home Applications